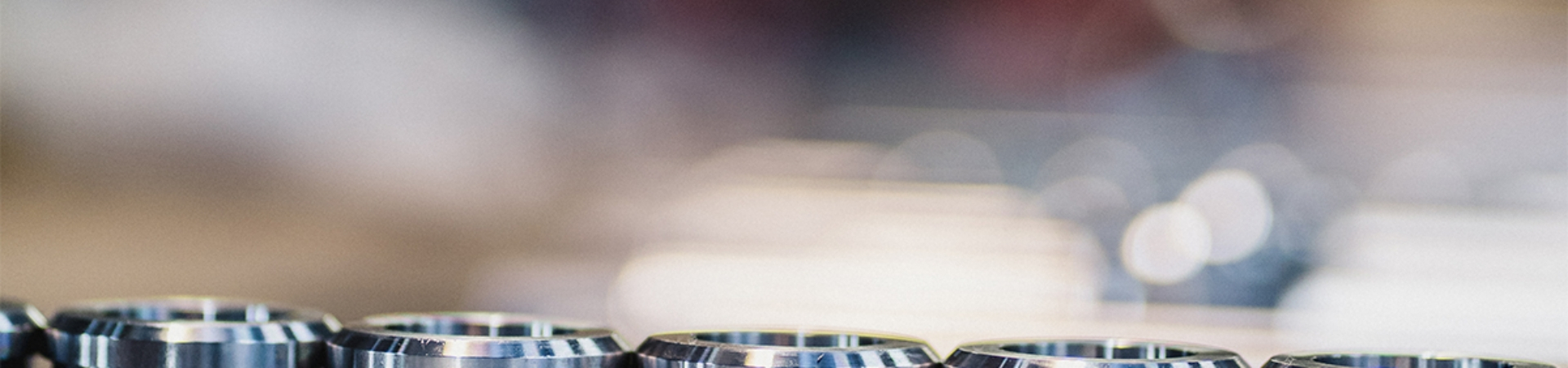
Venting the hydraulics

Things to know about venting the hydraulics
There are many reasons that it is necessary to vent the hydraulic system. Especially in the case of large pressure fluctuations, air inclusions in hydraulic oil can cause the so-called Diesel effect, in which extremely high tempe- ratures lead to oil aging and seal wear.
Another negative effect is that air diffuses through the seal material towards the low-pressure side. The pressure decreases steeply at the surface of the seal, which causes the air bubbles to expand abruptly, which can damage or destroy the seal. Depending on the scale of such „micro explosions“, it is possible that in a very short time even the surfaces of the sealing and running surfaces could be affected so badly that they appear like they would when abrasive wear has occurred .
Compressed air inclusions – which under high pressure are no longer visible – can cut the sealing surface like tiny knives when they brush over the seal.

In short:
Hydraulic cylinders – just like the hydraulic system as a whole – have to be vented carefully before they are put into operation. In order to make sure that there is no air remaining in any part of the hydraulic system, the application and the cylinders should be actuated a number of times with as low a pressure as possible; this will facilitate complete venting. For this reason AHP Merkle offers optional vents for almost all hydraulic cylinders.
The detailed procedure for venting hydraulic cylinders is provided in the chapter „Operating and maintenance instructions“
Caution: Because under certain circumstances air dissolved in the hydraulic fluid may be released, it is advisable to vent the system again when maintenance is performed.
Tip:
To allow complete venting of hydraulic cylinders, the venting screws should be placed at the highest point.